For more than 400 years, since the beginning of the Edo period, the Minabe-Tanabe region of southern Wakayama Prefecture has been celebrated as the source of ume, Prunus mume, of superlative quality. In December 2015, the Minabe-Tanabe Ume System was designated a Globally Important Agricultural Heritage System (GIAHS) by the United Nations Food and Agriculture Organization.
Effluent consisting of seasoning liquid used during the umeboshi (pickled ume) production process is so highly concentrated, with biochemical oxygen demand (BOD)* exceeding 100,000 mg per liter, that conventional aerobic wastewater treatment has a tough time dealing with it. The effluent is handled by industrial waste treatment companies contracted for the task, which is costly and burdensome for local umeboshi producers.
Sumitomo Heavy Industries Environment, a subsidiary of Sumitomo Heavy Industries, is engaged in water sewage and industrial wastewater treatment businesses. For its client Nakata Foods, a leading umeboshi producer, the company constructed a biogas power plant that uses the ume seasoning liquid effluent. Sumitomo Heavy Industries Environment developed the scheme jointly with Miyaso Chemical, a local industrial waste treatment and transportation company. As well as collecting and transporting the ume seasoning liquid from Nakata Foods and other umeboshi producers, Miyaso Chemical manages and operates the facilities. For its part, Sumitomo Heavy Industries Environment designed and installed the facilities, capitalizing on its long-cultivated water treatment technology.
Whereas much of the ume seasoning liquid had previously been discharged, at the new plant it is neutralized and its concentration adjusted, and then anaerobic wastewater treatment is applied. Furthermore, biogas that is a by-product of the treatment process is used for power generation. Under the feed-in tariff (FIT) program for renewable energy, the electricity is sold to recoup the cost of constructing the plant.
Although conventional wisdom has it that ume seasoning liquid’s high sugar content makes it unsuitable for anaerobic treatment, Sumitomo Heavy Industries Environment’s unique technology overcame this issue. Compared with conventional aerobic wastewater treatment, the treatment cost is slashed because the process is far less energy intensive and no excess sludge is produced. Kamitonda Town, where the plant is located, cooperated in terms of provision of the site for the plant and the well water necessary for the treatment. In fact, the entire community got behind the project, enthusiastically supporting the establishment of the plant. The biogas power plant treats the ume seasoning liquid effluent efficiently, thus minimizing the environmental impact and reducing the local industry’s burden.
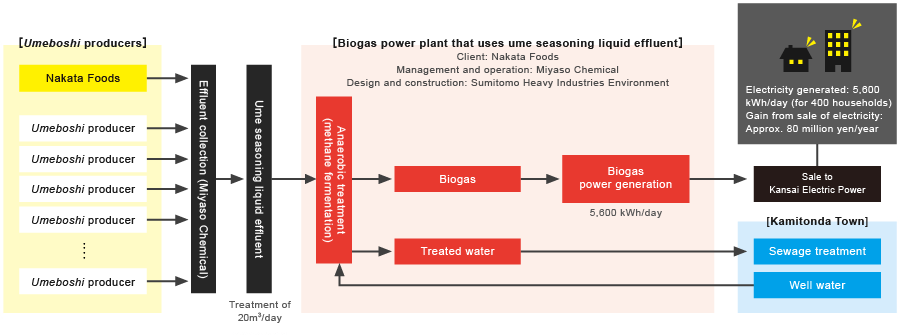
The plant started operation in April 2019. Initially, the plan calls for treatment of 8,000 tons out of about 60,000 tons of ume seasoning liquid effluent generated in Wakayama Prefecture per year. With an eye to sustainable community development, Sumitomo Heavy Industries Environment intends to bring the advantages of this technology to the attention of other local governments and industries facing similar challenges.